The Port of Paranaguá was the first Cargill site to install the DustControl. It continues to operate until today with no operator input and no maintenance. Cargill has purchased nine more DustControl systems, acknowledging that an investment in DustControl equipment is a great long-term investment.
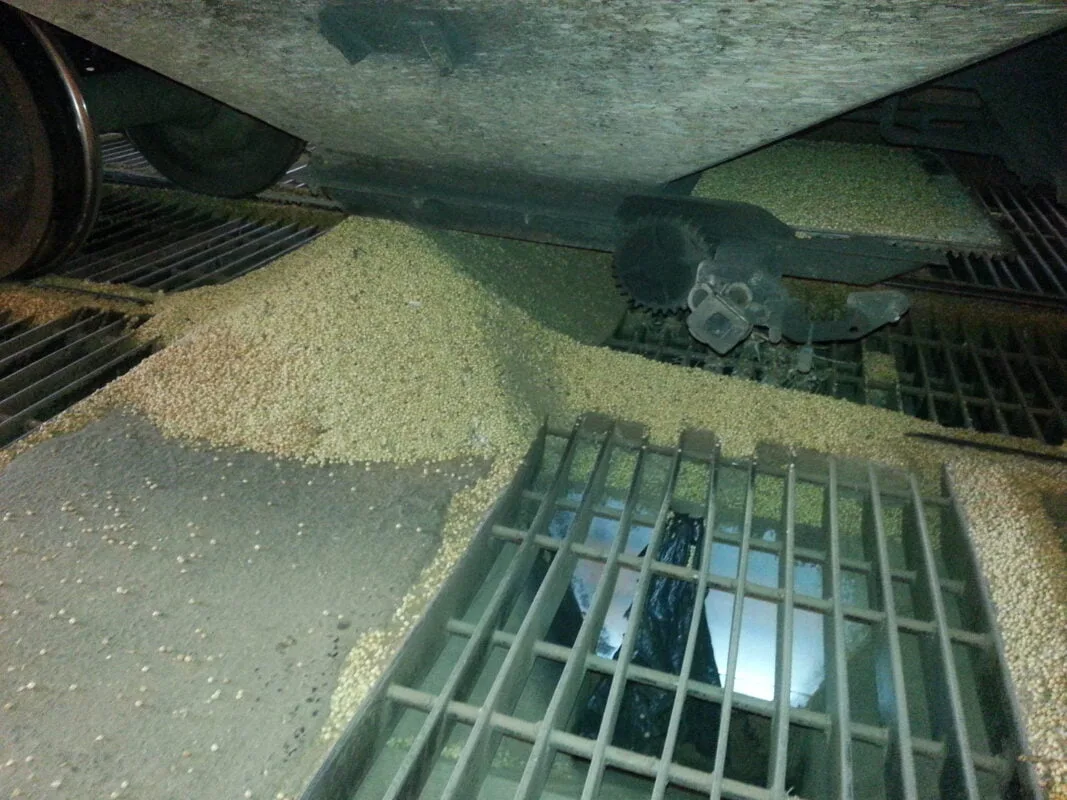
This photo was taken in 2017, ten years after the installation of DustControl. The current manager of the Cargill Paranaguá unit, did not believe that DustControl was in operations. All operators and neighbors of the hopper realized that there was no dust during unloading, but did not understand how. Only when our team went on site and showed that there was no dust because DustControl was installed.
Through various analyzes and surveys of our customers, we can say that the time of use, per hour is undetermined, this is yet another Wings Ltda system, which since its installation until today, continues to operate automatically, without maintenance.
Projects like this give us the total certainty that we are on the right path. The transportation of grains by trains is less polluting, and leaving the moment of unloading grains free of dust, we are sure of the continuity of the work in bringing greater benefit to the health of the planet.
Em outubro deste mesmo ano, implementamos mais um DustControl na nossa cliente/parceira Cargill em suas instalações em Ponta Grossa – Paraná.
Solving problems with dust in receiving hoppers is the purpose of the Wings DustControl system. It controls the emission of air into the atmosphere so that the dust remains with the product. There is no need for expensive filters that are costly to operate and ineffective.
O sistema DustControl não é um sistema flaps. O DustControl é composto por módulos que cobrem toda a moega abaixo da grade. Esses módulos têm 40 a 50 cm de profundidade e bicas que reduzem ligeiramente a velocidade do produto que entra na moega, mantendo as bicas cheias de produto para que o ar deslocado da moega passe pela coluna de produto nas bicas. Durante a passagem pelo módulo, o ar carregado de poeira perde velocidade e não é mais capaz de carregar a poeira, que permanece junto com o produto. O ar sai limpo do módulo. É a mais eficaz maneira de fazer despoeiramento! Não precisa de filtros.